What is Lean Manufacturing?
Lean manufacturing, also known as lean production, is a production method that focuses on maximizing productivity, while simultaneously minimizing waste, within a manufacturing process. Basically, it allows for the streamlining of workflows.ย ย
An integral part of improving business processes is minimizing waste. As a result, lean manufacturers can deliver value to the customer. Waste is considered as anything that doesn’t add value for the customers. For example, types of waste include activities, tasks, and products or services that involve time, money, and expertise that don’t create value for the customer.
The Benefits of Lean Manufacturing
Eliminates Waste
A huge benefit of adopting a lean manufacturing production method is that you’ll be able to reduce waste.ย As previously mentioned, it is important for businesses to minimize waste to improve business processes. This is because it can have a negative impact on costs, deadlines, and resources.ย
Improves Quality
Businesses can experience improved quality, thereby increasing their efficiency. This means that they can better compete and meet changing consumer behaviours.ย
Reduces Costs
Businesses that have better operations and management of materials will minimize the overproduction and surpluses of materials. Therefore, reducing storage costs.
Reduces Time
Businesses can save time by conducting efficient working conditions. For instance, this will allow for faster delivery of goods and services to the customer.
The Benefits of Lean Manufacturing
Eliminates Waste
A huge benefit of adopting a lean manufacturing production method is that you'll be able to reduce waste.ย As previously mentioned, it is important for businesses to minimize waste to improve business processes. This is because it can have a negative impact on costs, deadlines, and resources.ย
Improves Quality
Businesses can experience improved quality, thereby increasing their efficiency. In short, this means that they can better compete and meet changing consumer behaviours.
Reduces Costs
Businesses that have better operations and management of materials will minimize the overproduction and surpluses of materials. Therefore, reducing storage costs.
Reduces Time
Businesses can save time by conducting efficient working conditions. Forย instance, this will allow for faster delivery of goods and services to the customer.
The Five Lean Principles
Lean manufacturing has five core principles. These principles are used as a foundation to implement lean techniques within an organization.
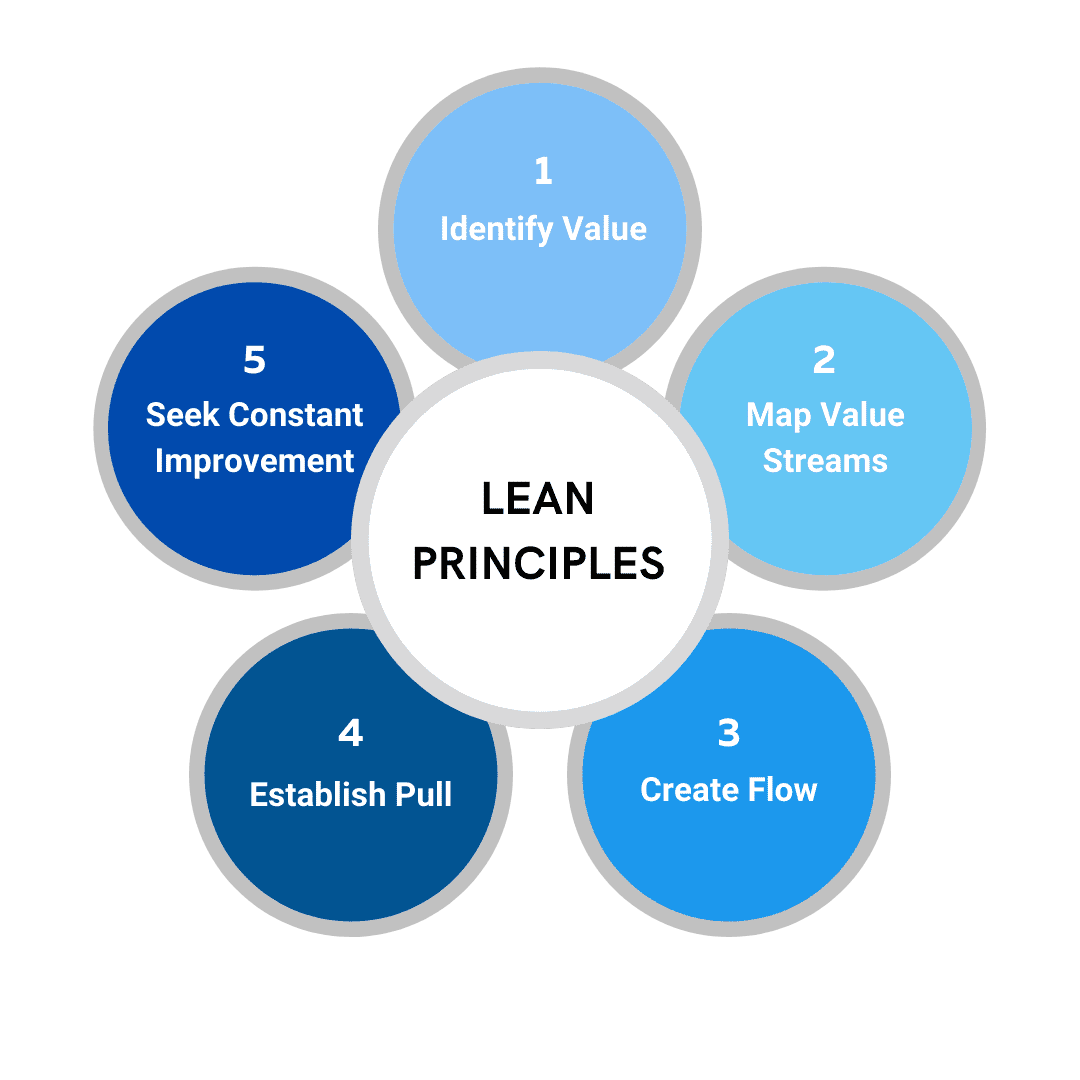
1. Identify Value
The first core principle of lean manufacturing is to identify value. Value can only be defined from the perspective from the customer. To clarify, it is how much the product or service is worth to them and/or how much they are willing to pay for the product or service. For example, questions to help identify value include how long does delivery take? How much does it cost? What is the benefit to the customer? Does it solve my customers’ problem?
2. Map Value Streams
The second core principle of lean manufacturing is to map your value streams. That is to say, once the value has been identified, the goal is to use it as a reference point and map all the relevant steps and activities involved in creating value for the customer. Furthermore, this helps to identify waste and improvements. As a result, you have a better chance of giving customers exactly what they want. Consequently, this will lead to the reduction of production costs.ย
3. Create Flow
The third core principle of lean manufacturing is to create flow. After waste is identified and eliminated from the value stream, the next step is to ensure that the remaining steps flow smoothly. For instance, there shouldn’t be any delays, interruptions, or problems. Some strategies that can assist in creating flow include dividing or modifying steps, balancing out the workload,ย promoting collaboration between different departments, and training your workforce to be flexible and versatile.
4. Establish Pull
The fourth core principle of lean manufacturing is to establish a pull system. This is established by producing products only when there is demand. In other words, it allows for just-in-time manufacturing or delivery. This means that products are only produced when they are needed and in the quantity that they are needed. As a result, production doesn’t need a head start and materials don’t need to be stockpiled. Therefore, it reduces costs for both the manufacturer/producer and the customer.
5. Seek Constant Improvement
Principles one to four are essential for identifying and eliminating waste. However, the fifth core principle of lean manufacturing is the most important: making lean thinking and continuous improvement a part of an organization’s culture. In sum, it is essential that all team members within each level of the organization are involved in implementing lean.ย
TheLeanSuite's Lean Manufacturing Software
Some organizations offer platforms that solely focus on only one tool, for example employee engagement or safety management. On the other hand, we offer aย lean manufacturing software that contains multiple built-in lean manufacturing tools.
TheLeanSuite features most, if not all, of the relevant lean manufacturing solutions required to increase productivity and efficiency within an organization’s shop floor. As a result, it enables manufacturers and factories to apply lean principles and techniques into their internal processes and helps them foster a continuous improvement culture.ย