Continuous improvement is a philosophy rooted in the belief that operations, no matter how efficient, can always be enhanced. Moreover, this concept emphasizes the power of incremental changes and small improvements that collectively lead to significant improvements over time. In this blog, we get into the essence of continuous improvement, exploring its principles, methodologies, and the transformative impact it holds for organizations seeking to not just survive, but thrive in todayโs dynamic landscape.
What is continuous improvement?
Continuous improvement, often encapsulated by the Japanese term “Kaizen,” is a strategic approach that seeks to enhance processes, products, or services through ongoing, incremental improvements. Rather than aiming for massive changes or breakthrough innovations, continuous improvement focuses on making small, consistent changes that can lead to significant improvements over time.
This method relies heavily on the involvement of everyone within your organization. In other words, continuous improvement encourages a culture where feedback is valued and every employee feels empowered to contribute ideas for betterment. By continuously seeking ways to increase efficiency, reduce waste, and improve quality, you can adapt more swiftly to changing market demands and maintain a competitive edge.
The continuous improvement cycle
The PDCA Cycle, which stands for Plan-Do-Check-Act, is among the most widely used tool for process improvement and the continuous improvement model. So much so that itโs been referred to as the continuous improvement cycle instead. Itโs a four-step iterative method used to control and continuously improve processes and products. The four steps are:

1. Plan
This initial stage involves identifying a problem or a goal and planning a change that could improve the situation. It requires a detailed understanding of the current process and the issue at hand. In other words, the planning phase should include setting clear objectives, defining the steps necessary to achieve them, and establishing metrics for success.
2. Do
During the Do phase, the plan is implemented on a small scale to test its effectiveness. This could involve making changes to a process, introducing new methods or tools, or implementing a new strategy. The key here is experimentation: trying out the planned change and collecting data on the results.
3. Check
In the Check phase, the outcomes of the Do phase are evaluated. This involves comparing the collected data against the expected outcomes to see if the change has led to improvement. In essence, this step is a time for reflection and analysis, looking at what worked, what didn’t, and why.
4. Act
Based on the analysis and learning from the Check phase, the Act phase involves making decisions about the next steps. If the change was successful, it might be implemented on a larger scale or become a new standard practice. If the change didn’t lead to improvement, it might be adjusted or abandoned, and a new PDCA cycle can begin with a revised plan.
The five key principles of continuous improvement
There are five key principles that lie at the core of this philosophy. These principles ensure that improvements are manageable, inclusive, strategic, and impactful. As a result, this makes the journey towards excellence a collective and rewarding endeavour.

1. Improvements are based on small changes
This principle emphasizes that even minor adjustments can accumulate to produce substantial outcomes. By focusing on small, manageable changes, you can avoid the pitfalls of attempting overly ambitious changes that are hard to implement and sustain.
2. Ideas must come from employees
Employees, being on the front lines, have firsthand insight into the day-to-day operations. Therefore, they’re a valuable source of innovative ideas. So, by encouraging them to contribute suggestions, this fosters a sense of employee involvement and empowerment.
3. Employees take ownership of and are accountable for improvement activities
This principle ensures that those who suggest changes are also involved in the implementation and assessment of improvement activities. Essentially, it instills a sense of responsibility and pride in the outcomes, driving further engagement and innovation.
4. Improvements are aligned with strategic goals
For continuous improvement efforts to be effective, they must support the broader objectives of your organization. This alignment ensures that every small change contributes to the overarching vision. Thus, maximizing the impact of these improvements.
5. Improvements should be measurable and repeatable
To gauge the effectiveness of continuous improvement initiatives, they must be quantifiable and capable of being replicated. This allows you to track progress, validate the impact of changes, and apply successful strategies consistently across different areas.
Why use a continuous improvement process?
The philosophy of continuous improvement is much more than a set of tools and techniques; itโs a mindset that can transform your organization. Here are some of the main benefits of the continuous improvement process.
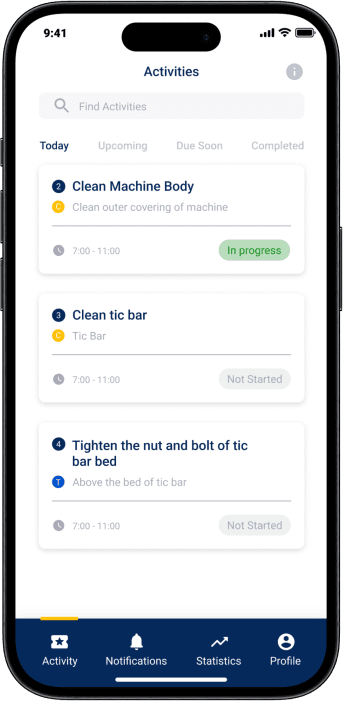
Reduced waste
One of the significant benefits of the continuous improvement process in any organization is the reduction of waste. By systematically evaluating and refining processes, you can identify inefficiencies that donโt contribute to your customer’s value perception or your bottom line. Whatโs more, this ongoing improvement process allows for the streamlining of operations. Consequently, this makes them more efficient and cost-effective.
Improved quality
The continuous improvement process places a strong emphasis on quality. Through constant monitoring and refining of processes, you can enhance the quality of your products and services. This method involves ongoing effort from everyone in your organization, from the top management to the front-line employees. In essence, it encourages a team approach to problem-solving. As a result, defects and errors are reduced, and the overall reliability of your product or service increases, which is crucial for maintaining competitive advantage.
Improved customer satisfaction
By consistently working to improve products and services, you can better meet your customers’ needs and expectations. High-quality, reliable products and efficient service contribute to a positive customer experience, which is essential for building customer loyalty and attracting new clients through word-of-mouth. In short, satisfied customers are more likely to return and recommend your business to others, driving growth and profitability.
Improved employee engagement
The continuous improvement process fosters an environment where your employees are encouraged to share their ideas and suggestions for better ways of working. This sense of involvement and empowerment leads to higher levels of job satisfaction and engagement. When your employees see that their contributions can lead to positive changes, it boosts morale and fosters a sense of ownership and pride in their work.
Fosters a culture of innovation and agility
Adopting a continuous improvement mindset instills a culture that values innovation and flexibility. In todayโs fast-paced world, the ability to quickly adapt to changes and innovate is crucial for survival and growth. So, by continually improving, you can respond more swiftly to market changes, customer needs, and technological advancements. This culture of agility and innovation can make you more resilient and better positioned to seize new opportunities.
Common continuous improvement tools and methods
Six Sigma
Six Sigma is a data-driven approach and methodology for eliminating defects in any process. Created by Motorola in the 1980s, this methodology employs quality management techniques, predominantly empirical and statistical methods, and establishes a dedicated group of individuals within the organization who are experts in these methods.
Every Six Sigma project in an organization adheres to a set sequence of steps and includes specific financial objectives (such as reducing costs or increasing profits). Basically, the primary aim is to enhance process quality by pinpointing and eliminating defect causes while reducing variability in manufacturing and business operations.
Lean Manufacturing
Lean Manufacturing, or also known as the Lean Methodology or Lean Process Management, is a systematic approach to minimizing waste within manufacturing systems, while simultaneously improving productivity. Originating from the Toyota Production System (TPS), it emphasizes the creation of more value for customers with fewer resources. This is made possible by optimizing the flow of materials and information.
Tools such as 5S, Poka-Yoke (error-proofing), and value stream mapping are integral to the implementation of Lean. By focusing on value from the customer’s perspective, organizations work to continuously improve their processes by eliminating anything that doesn’t add value.
Kanban Method
The Kanban Method is a visual system for managing work as it moves through a process. Kanban visualizes both the process (the workflow) and the actual work passing through that process. Essentially, the goal of Kanban is to identify potential bottlenecks in your process and fix them so work can flow through it cost-effectively at an optimal speed or throughput. By making workflow and processes visible, the method fosters better communication and collaboration among team members.
Total Quality Management (TQM)
Total Quality Management (TQM) is a comprehensive strategy for achieving long-term success. It emphasizes continuous improvement across all areas of an organization as an ongoing process, rather than a short-term objective. What’s more, it advocates for the involvement of management, workforce, suppliers, and even customers, in order to meet or exceed customer expectations.
At the heart of TQM is the concept of doing things right the first time. However, when mistakes do occur, it’s important to learn from them to prevent future issues. TQM combines fundamental management practices, existing continuous improvement methods and efforts, and technical tools within a structured method that focuses on continuous improvement. The philosophy behind TQM is to reduce the production of defects, to reduce unnecessary business costs, and to meet and exceed the needs and expectations of customers. Thereby, ensuring their satisfaction and loyalty.
Root Cause Analysis (RCA)
Root Cause Analysis (RCA) is a method of problem solving used for identifying the root causes of faults or problems. Itโs used in many industries to help organizations identify the underlying reasons why a problem occurred in the first place. By addressing the root cause, rather than merely tackling the symptoms of the problem, you can prevent problems from recurring. Techniques used in RCA include the 5 Whys Analysis and the Fishbone Diagram (also known as the Ishikawa Diagram or Cause and Effect Diagram).
What is a continuous improvement culture?
A continuous improvement culture is a business philosophy that encourages ongoing, incremental enhancements in processes, products, or services, driven by the collective effort of all employees. It revolves around the belief that there is always room for incremental improvement, no matter how small, in every aspect of the organization’s operations.
How to foster a culture of continuous improvement
To foster a continuous improvement culture, there are seven fundamental steps you can take to transform your company culture and organization, making it more agile, innovative, and competitive.

1. Lead by example
Leadership plays an important role in setting the tone for a culture of continuous improvement. That is to say, when leaders themselves are committed to personal and professional growth, they inspire their teams to adopt the same mindset. Therefore, by demonstrating a willingness to learn, adapt, and improve, leaders can effectively model the behaviours they wish to see throughout the organization.
2. Collect employee suggestions
Empowering employees by actively seeking their input encourages a sense of ownership and engagement. When individuals feel their ideas are valued and considered, theyโre more likely to contribute to innovative solutions and improvements. So, establishing a structured process for collecting, evaluating, and implementing suggestions ensures that good ideas are recognized and acted upon.
3. Be open-minded
Fostering an environment where new ideas are welcomed and not immediately dismissed is crucial for your continuous improvement journey. Being open-minded means being willing to consider different perspectives and approaches, even those that challenge the status quo. This openness can lead to breakthrough innovations and improvements in current processes that might otherwise be overlooked.
4. Provide instant feedback
When you actively seek suggestions from your employees for improvement opportunities, following up on each oneโeven the bad onesโis crucial. This action not only helps to foster an inclusive and dynamic workplace culture, but also encourages your employees to continuously identify and share improvement opportunities. In essence, prompt follow-ups ensures that no potential for improvement is overlooked and that your employees feel heard and valued.
5. Make improvement easy
Removing barriers to improvement is essential for fostering a culture of continuous growth. This can involve simplifying processes, providing the necessary tools and resources, or offering training and development opportunities. When improvement is made easy and accessible, it becomes a natural part of daily work.
6. Recognize and reward your employees
Acknowledgment and appreciation are key motivators for continued effort and engagement. Recognizing and rewarding employees for their contributions to improvement not only reinforces positive behaviour, but also builds a sense of community and shared purpose. Types of rewards can be as simple as public acknowledgment or as substantial as promotions and bonuses.
7. Support cultural change
Lastly, creating a culture of continuous improvement requires ongoing support and reinforcement. For instance, this can involve regularly revisiting goals, celebrating milestones, and continuously communicating the value of improvement efforts. Support for cultural change also means being patient and persistent. This is because developing a new culture takes time and sustained effort.