Customer Showcase: Whirlpool Corporation
Today, paperless manufacturing is essential in a business landscape that has become increasingly digital. Transforming into a paperless factory enables you to to be more agile and better react to the ever changing market demands. However, there are still many manufacturers who are still either using paper-based processes or even endless amounts of spreadsheets to mange their operations. This was Whirlpool Corporation.
About Whirlpool Corporation
Headquartered in Benton Charter Township, Michigan, United States, Whirlpool Corporation is an American multinational manufacturer and marketer of major home appliances. In fact, they are considered to be one of the most reliable appliance brands on the market. Whirlpool serves customers worldwide and has an iconic brand portfolio that includes Whirlpool, KitchenAid, Maytag, Consul, Brastemp, Amana, Bauknecht, JennAir, Indesit, Yummly and InSinkErator.

Approach
Realizing that the outdated solutions were the culprit for the inefficiencies, Whirlpool Corporation leveraged the LeanSuite’s Continuous Improvement System.
Continuous Improvement System
The Continuous Improvement System is an end-to-end project management software designed for the modern manufacturer looking to manage their continuous improvement projects in the cloud. Instead of spending hours weekly manually pitching projects, searching through spreadsheets to find the right employee with the right skills and competencies to tackle the projects, sifting through numerous filing cabinets to find relevant project information, and so on and so forth, Whirlpool Corporation leveraged the Continuous Improvement System to do the hard lifting for them.
Continuous Improvement System Features
Some features of the Continuous Improvement System that proved to be useful to Whirlpool Corporation include:
- 1. Workflow Builder: automate routine tasks and create workflows your way with custom rules and trigger
- 2. Template Builder: create digital templates within minutes with an easy-to-use drag-and-drop interface
- 3. Workload Management: ensure everyone on your team is assigned the right amount of work
- 4. Delay Management: identify the root cause of your project delays and get them back on track
- 5. Knowledge Base — Best Practices: document and share effective and efficient guidelines and procedures to carry out your projects
- 6. Knowledge Base — Lessons Learned: document and share learnings from both project failures and successes
- 7. Knowledge Base — Maintenance Preventative Information (MPI): document and share maintenance-related improvements
Results
By leveraging the LeanSuite’s Continuous Improvement System, Whirlpool Corporation was able to:
- 1. Operate in real-time. Instead of physically search for answers or using the copy machine to transfer documents from one, they just clicked around the system to find what they needed immediately, knowing that it was real-time information. What’s more, instead of spending weeks managing a project from start to finish, they were able to create, manage, and implement multiple continuous improvement projects at once, all in real-time.
- 2. Increase productivity. By leveraging a digital, cloud-based solution, this means less filling in and filing forms, less manual tracking on endless spreadsheets, and more time for creating and implementing projects that added value for the customer.
- 3. Improve data accuracy. To start and complete a project, there are many different forms that are collected and managed throughout the entire process. By leveraging the Continuous Improvement System, Whirlpool Corporation was able to keep their data accurate and up to date, in real-time.
- 4. Improve visibility. The Continuous Improvement system enabled Whirlpool Corporation to view:
- — Who is working on what
- — What is currently being worked on
- — What projects are delayed
- — When maintenance is being scheduled, and on what
- — What is costing you a lot of money
All this then assisted in them winning the 2022 Manufacturing Leadership Award for the category of Enterprise Integration and Technology.
Recognizing Whirlpool Corporation: 2022 Manufacturing Leadership Award Winner
On June 29, 2022 in Marco Island, Florida, the National Association of Manufacturers’ (NAM) Manufacturing Leadership Council recognized Whirlpool Corporation as a winner in the 2022 Manufacturing Leadership Awards Gala for their outstanding efforts in two project categories: Operational Excellence, and Enterprise Integration and Technology. The award was given for their Project Tracking System and its Global Kaizen Power Pitch project.
NAM is the largest manufacturing association in the United States and represents both small and large manufacturers in every industrial sector in all 50 states. Founded in 2008, the Manufacturing Leadership Council is a division of the NAM. Its mission is “to help senior executives define and shape a better future for themselves, their organizations, and the industry at large by focusing on the intersection of critical business and technology issues that will drive growth today and in the future.” Whirlpool Corporation joined the Manufacturing Leadership Council in 2018, and this marks the first time the company was honoured with MLC awards.
Project Tracking System
Whirlpool Corporation’s Project Tracking System gives their project leaders complete visibility into all current and future projects across 14 manufacturing plants located throughout the United States and Mexico. The Project Tracking System is a project management tool that integrates project leaders’ skills, competencies, and workload to assign the right leader to the right project. It also enables them to track the status and progress of tasks within each project and manages root cause of delays.
Project tracking is important because it allows users to effectively see what has been accomplished so far, which tasks still need to be completed, which roadblocks they have faced, and what resources they need to overcome them in real-time on a web or cloud-based platform.
Global Kaizen Power Pitch
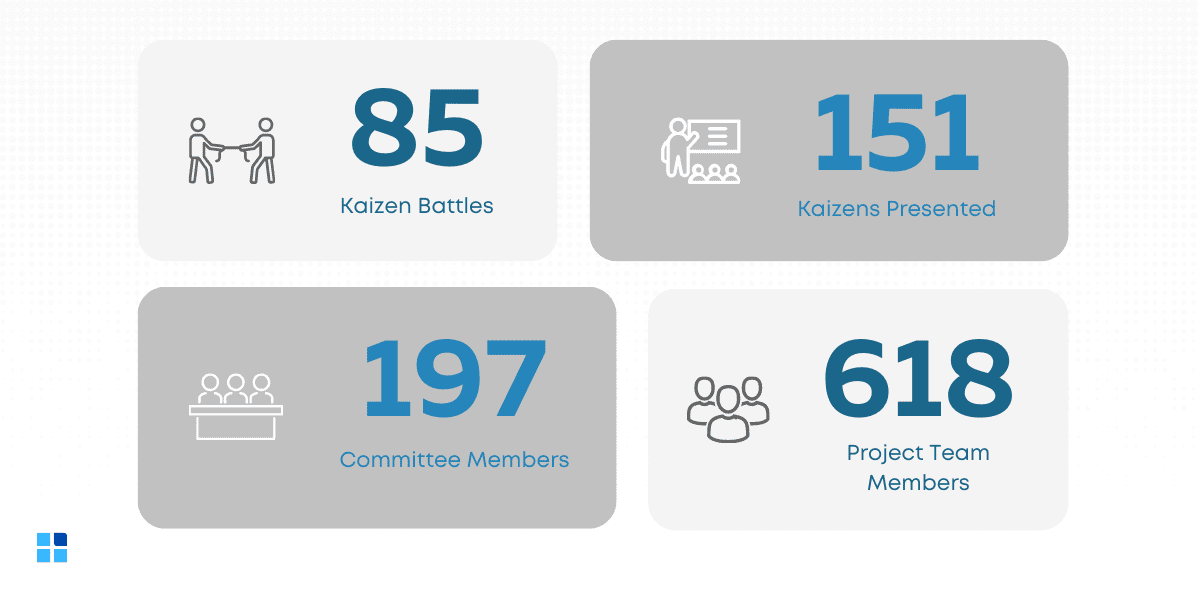
The Global Kaizen Power Pitch is a competition that was created for manufacturing plants to share best practices, technological tools, methodological knowledge, and examples with each other. As a result, manufacturing practices that were put into place because of the competition resulted in millions of dollars in savings at the plants. The Global Kaizen Power Pitch also allowed colleagues from across the world who worked on similar projects to connect with each other and gave them the opportunity to network with people whom they don’t usually meet.
Whirlpool Corporation participated in the first global event that took place between May 2021 and January 2022 where outstanding manufacturing plants that delivered manufacturing excellence were recognized. The Senior Director of the North American Region (NAR) of Operational Excellence, Ramsey Alijahmi recognized both of Whirlpool’s projects to be “incredibly important to [their] manufacturing team and the improvement of our processes in the North American Region (NAR), as well as across the globe”.
To learn more about the Manufacturing Leadership Award, click here.
To view Whirlpool Corp.’s original article, click here.