Lean manufacturing and continuous improvement go together, hand-in-hand. But, while they work together to create a more productive and efficient shop-floor, each has their own set of core principles. In today’s blog, we detail the three core principles of continuous improvement. But first, let’s briefly get into what continuous improvement is.
What is Continuous Improvement?
Continuous improvement is an ongoing process of collaboratively identifying opportunities to streamline work and reduce waste. In other words, it requires all employees at all levels of an organization to contribute to making continual, gradual improvements to systems, processes, products, or services. The purpose of continuous improvement is to drive efficiency, improve quality, and optimize value delivery while simultaneously minimizing waste and other inefficiencies. What’s more, this process is driven by ongoing employee feedback, teamwork, and data.
Continuous improvement is considered to be an important aspect of many management systems such as Lean, Six Sigma, and Total Quality Management (TQM). In Lean in particular, continuous improvement is also known as Kaizen. It is a Japanese business philosophy that focuses on the processes that continuously improve operations and involves all employees to improve productivity and efficiency. The overall goal of Kaizen is to make small, incremental changes over a period of time to ultimately create improvements within an organization. That is to say, the Kaizen philosophy recognizes that small changes now can have huge impacts in the future. Suggestions for improvement opportunities should come from any and all employees. In short, Kaizen believes that everyone is responsible for the company’s success and therefore, they should always try to improve the business model.
The 3 Core Principles of Continuous Improvement
The continuous improvement approach can be applied to all industries and to businesses of all sizes. However, there are several principles that guide the continuous improvement model. Listed below are the three core principles of continuous improvement:
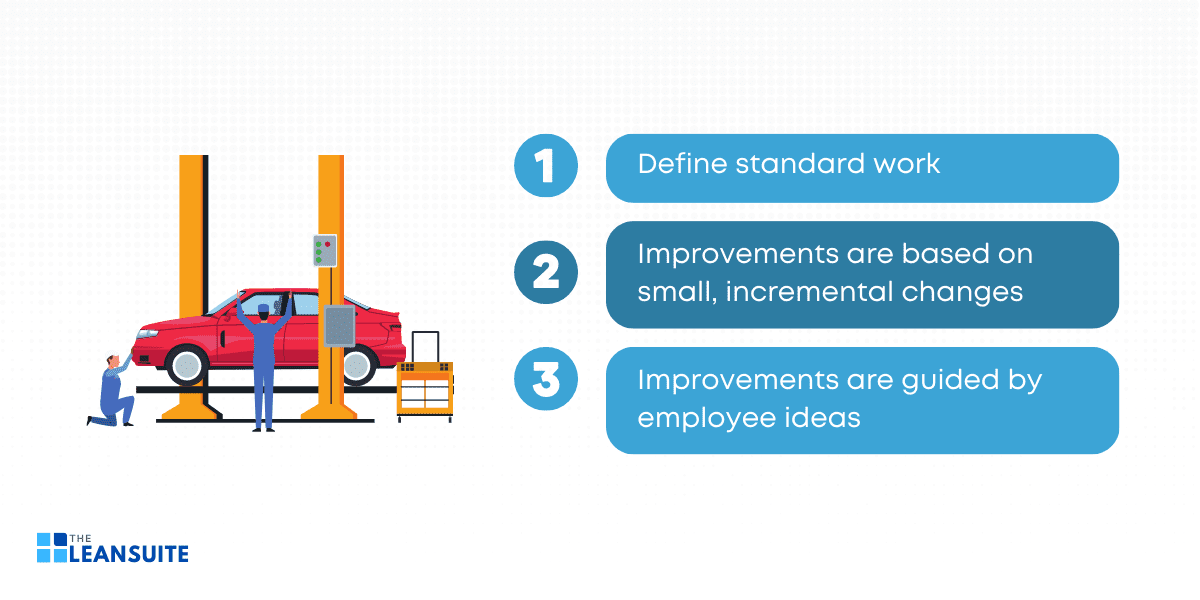
1. Define standard work
Define standard work is often one of the the most overlooked principles of continuous improvement. However, it is the foundation of continuous improvement. Many organizations face a common challenge: they don’t know how work is being done in their companies. As a result, work cannot be improved if it is unclear what that work is or what it looks like. Therefore, any continuous improvement initiatives requires you to put the effort into identifying, documenting, and digitizing your workflows to create standard work and visualize how work is performed. Once those steps are completed, only then you can get started on process improvement.
2. Improvements are based on small, incremental changes
One of the most fundamental principles of continuous improvement is that improvements are based on small, incremental changes. This principle is important because small changes are easier to adapt to than big changes. By approaching change in small, incremental steps, implementing continuous improvement decreases the fear factor and increases the speed of improvement. What’s more, addressing smaller elements of a complex problem may reveal simple solutions to the bigger problem.
3. Improvements are guided by employee ideas
Continuous improvement should not come from top management, leadership teams, or outside consultants. Instead, it should come from the employees who deal with processes daily and know their operations well. This bottom-up improvement model is one of the most effective principles of continuous improvement because employees are closest to the problems. Therefore, they are better suited to identify improvement opportunities. For instance, by simply asking “how could you improve this step of the process?” this could yield creative ideas that save minutes or dollars, make operations safer, or eliminate inefficiencies.
Continuously Improve with the LeanSuite
The LeanSuite’s Continuous Improvement System provides the solution you need for efficient continuous improvement and project management that delivers results. With the Continuous Improvement System, you can gain end-to-end visibility on all your business projects, ensuring that you can analyze the changes you’ve applied and assess whether your continuous process improvements are working and where you should prioritize your efforts next.